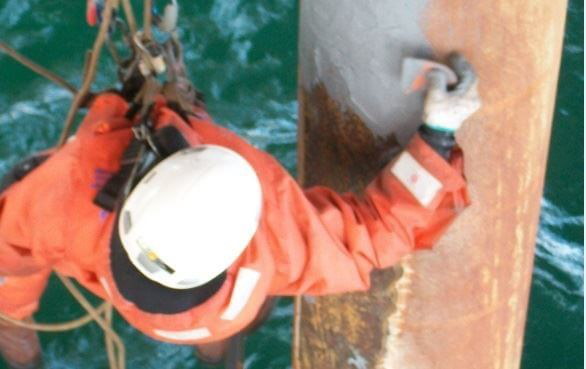
Takeaway:When a pipe ruptures or a tank leaks, rapid repair is essential. Historically there have been few repair materials that can overcome costly surface preparation requirements, surface contaminants, slow curing, wet-cold conditions, and other common problems.
One of the major challenges faced by maintenance engineers across many industries is the limited amount of time in which urgent repairs must be carried out. In the real world, when a rapid repair is required, ideal surface preparation is not always an option.
Many available repair solutions are not compatible with minimal surface preparation, and therefore can often lead to failure. Producing faster curing epoxy materials and those curing at lower temperatures have long been goals of protective coatings and composites suppliers. Improved production rates, reduced time for job completion and the ability to apply materials at lower temperatures and extend equipment life are attractive to the applicator, end user and owner alike.
A critical aspect of any repair material is its ability to adhere to the substrate. Standards for coatings and repair composites require at least a 75 micron grit-blasted surface profile, and SA 2.5/NACE No. 2 /SSPC-SP 10 near-white metal surface cleanliness. It is critical that the substrate be clean, dry and free of oil and salt contaminants. Unfortunately, meeting all these requirements in the field can often be difficult, if not impossible. (For more on this subject, see Novel In-situ Repair of Leaking Oil Tanks Solves Maintenance Dilemma.)
Limitations of Common Materials
Common problems with available materials result in longer downtime intervals, higher costs and higher incidence of failures. Commercial adhesives do not tend to perform well when bonding to oil-contaminated substrates in wet or aquatic environments, especially at low temperatures.
Common surface-tolerant bonding adhesives are slow to cure and have relatively low bond strengths compared to adhesives formulated for dry applications. Traditional acrylic adhesives have longer set times that slow assembly processes and lower impact resistance, resulting in brittle bonds. These materials also have a limited shelf life and high odor levels that can cause health and safety concerns. And most polymer repair solutions are not compatible with minimal surface preparation, and can often lead to failure.
These systems fall short for use in adverse conditions for a variety of reasons. In two-component adhesive systems, the chemically reactive components needed for curing generally react low in the presence of water and oil, and thus create poor-quality bonds. Light curable adhesives generally require external heat sources, making them less desirable from a logistical standpoint. Few thermally cured adhesives result in rapid, high-strength adhesion, and even fewer function in high-moisture environments. Moisture reduces adhesion and low water temperatures reduce exothermic cure for underwater adhesives. As a result, underwater adhesives either cure poorly or require long cure times to obtain sufficient adhesive properties.
Latest Technology Development
New polymeric technology has led to the development of an epoxy-based paste grade material called BSC-1999, which addresses on-site emergency repair challenges. It can be applied on oily, wet and even underwater surfaces, which eases some of the typical surface preparation requirements.
With a high level of tolerance to surface contamination and excellent adhesion to manually prepared substrates, the material allows the epoxy to penetrate the profile and create a strong mechanical bond without grit blasting. The minimal surface preparation requirement is SSPC-SP 11 Power Tool Cleaning to Bare Metal.
The cold curing system achieves excellent adhesion where grit blasting is not possible, including problem areas such as water, oil and fuel leaks on storage tanks, pipework, transformers and sumps. After mixing the two components, BSC-1999 cures rapidly even at temperatures as low as 41°F (5°C).
The ability to apply the material in high-moisture and underwater environments makes it suitable for the long-term repair of offshore structures, marine vessels, splash zones and coastal structures. Ship hulls, rudders, propellers and ballast tanks can be repaired without taking the equipment out of service.
Surface Tolerance, Cure, and Mechanical Strength
When applied to contaminated ground mild steel surfaces prepared in accordance with SSPC-SP11/ISO 8501-01 St3, BSC-1999 demonstrates excellent adhesion to surfaces contaminated with an extensive range of oils and fuels.
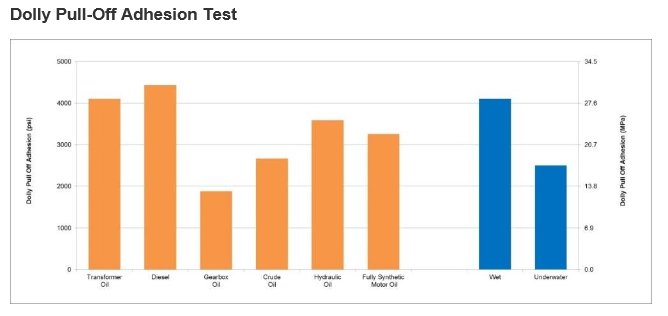
Figure 1 shows the results of the Dolly Pull-Off Adhesion test when applied to oil-contaminated, wet, and underwater surfaces, tested in accordance with ASTM D4541. (This test and others are discussed in 4 Types of Tests that Measure the Strength of a Coating.) From left to right, the orange bars in the graph below show the adhesion rates for transformer oil, diesel, gearbox oil, crude oil, hydraulic fluids and synthetic motor oil. The blue bars show performance in wet and underwater conditions.
Conclusions
Product suppliers, applicators, maintenance engineers and asset owners alike have long-faced the challenge of reducing the level of high-cost surface preparation without degrading the performance of the repair material. To overcome this apparent disparity between levels of cleanliness and product performance, many new products are being developed.
New technology in polymeric materials has led to the development of a fast cure epoxy-based product, which offers new opportunities when ideal surface preparation of the metallic substrate cannot be achieved due to lack of time or resources. (For more information, be sure to read Designing & Testing a New ISO/ASTM-Compliant Composite Repair Solution.)
Where conventional repair composites would be ineffective and perform poorly, the new technology bonds tenaciously onto steel substrates even when surface preparation is minimal or if the substrate is heavily contaminated with oil or water. BSC-1999 provides a cost-effective repair that can reinstate equipment for years of service.