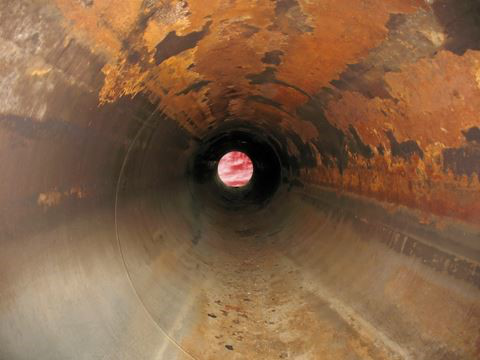
Takeaway: Carefully designed coatings, combined with cathodic protection and pipeline operating parameter controls, can help reduce pipeline corrosion.
Introduction
The longest pipelines are buried pipelines. They transport different petro products such as crude oil and natural gas, wastewater, potable water and other liquids, significantly influencing the economies of the developed countries as well as the developing countries. Corrosion of internal and external surfaces of pipelines is a leading cause of failure of buried pipelines. Apart from huge financial losses due to damaged assets, corrosion causes catastrophic failures, accidents and loss of precious lives. In case of potable water systems, corrosion can lead to disruption, wastage and supply of water of inferior quality.
Soil Condition
Due to contact with soil, the buried pipes face an environment that can change due to climatic and other factors in an abrupt manner. Methods adopted to lay the pipeline may at times damage the coatings provided on external surfaces. (For more information, see An Intro to Pipeline Corrosion and Coatings.) Even the slightest damage to coating can cause the onset of localized corrosion.
Low electrical resistivity of the soil helps it to act as an electrolyte in the following cases:
·When a part of a pipeline is laid on undisturbed local soil directly, and some part is laid on backfilled dissimilar soil, with uncompact earth containing excess oxygen.
·Long pipeline laid inside totally dissimilar soils.
·Sulfates, chlorides and other acidic contents are present in soil.
·Soils with clay content and moisture.
Soils with high sand content are less corrosive as they have higher electrical resistance. Shifting of soils can add to severity of corrosive pipe damage. Corrosive chlorides in soil result from tidal flows or ocean currents carrying saltwater droplets up to several miles away from the seashore. Soils with fuel-generated combustion products containing sulfur compounds and nitrogen result in reduced resistivity and higher corrosion potential.
Even alkaline elements such as sodium, magnesium and calcium lead to higher corrosion potential, whereas granular types of soils reduce the corrosion potential.
Moisture content of the soil depends upon the climate as well as the ground water level. Shifting ground water levels can result in higher corrosion. Even the temperature of the moist air affects corrosive reaction. At lower temperatures below freezing point, soil resistivity is high and corrosion potential is low. Generally soil properties such as electrical resistivity, organic content, sulfates, chlorides and pH value determine the soil corrosion potential.
Disturbed soils (filled soils) contain higher amount of oxygen. Oxygen at a cathodic region supports vigorous corrosion. Undisturbed soil has lower oxygen content. Soil aeration influences the availability of the moisture and oxygen necessary for the electrochemical reactions leading to corrosion of metallic pipe surfaces. (For further reading check out An Introduction to Soil Corrosion.)
Types of Corrosion Found in Buried Pipelines
· Uniform corrosion occurs at uniform rate over most of the surfaces throughout the pipe lengths.
· Pitting is the case of extreme localization of corrosion reaction due to hostile local environment.
· Erosion and cavitation corrosion mainly occurs on inside surface, due to contaminants as well as collapsing of vapor bubbles on the pipe wall, due to pressure changes in the liquids and turbulent flow conditions, which can be reduced by redesigning flow parameters.
· Intergranular corrosion occurs around the metallic grain boundaries in the metallic pipelines.
· Stress corrosion cracking of pipelines is caused by hostile environment and residual stresses, load stresses and climatic conditions.
Corrosion of Water and Sewage Pipes
Modern water pipes are generally made of ductile iron, but older pipelines could be mostly made of grey cast iron. These pipes are used for potable water systems, sewage, raw water, and some chemical applications.
Grey cast iron pipes fail due to graphitization corrosion. Residual graphitic flakes get interspersed with ferrous oxides, weakening the mechanical strength and making the material susceptible for failure due to hydraulic impulse or other mechanical load stresses. Apart from graphitization they also fail due to localized pitting corrosion, depending upon the soil conductivity for electric current flow during electrochemical reactions.
Galvanic corrosion results from use of dissimilar metals of galvanic series such as ductile iron and copper which becomes cathodic to iron.
Microbiological Corrosion
Buried metallic pipes are also prone to microbiological corrosion. Both aerobic type as well as anaerobic type of microbes (bacteria) can enable and accelerate the corrosion rate enormously. Certain types of sulfate reducer bacteria are responsible for enabling corrosion damage in presence of sulfur compounds. Anaerobic microorganisms have ability to release oxygen from compounds such as carbonates and sulfates for corrosion reactions, which will take place even if dissolved oxygen is not readily available. Microbe influenced corrosion is found to be accelerated by more than ten times, as compared to pipes with sterile contents. (Read more on this subject in Testing for Microbiologically Influenced Corrosion in Pipelines.)
Different soils, across the pipe length and depth, can aggravate corrosion, for example when a part of a pipeline is laid in sandy soil and the other part is installed in clay type of soil. These result in formation of anodic and cathodic cells on the same pipeline. However when the pipe lengths are joined through rubber gaskets, the electric circuit gets broken and pipe lengths may remain isolated from each other.
Corrosion Protection of Buried Pipes
External coatings for buried pipelines require the following properties:
· Negligible permeability
· Good electrical and electrochemical resistance
· High adhesion to the pipe's surface
· Flexibility
· Good impact strength
· Scratch resistance and abrasion resistance, to protect against damage during handling, testing, transport, laying and other site activities
· Not prone to cathodic disbondment
· Resistance to changes in soil and thermal stresses
· Resistance to cracking
Different types of barrier coatings are adopted for protection of buried pipelines. The types of coatings include:
· Loose polyethylene jacketing
· Epoxy coating
· Bituminous coal tar based coatings
· Polyurethane coatings
Loose Polyethylene Jacketing
For water pipes laid in corrosive sites like landfills, polyethylene encasements are commonly used. The advantages include ease of installation, low maintenance cost, low failure rates.
However the polyethylene encasement may get damaged during installation. It softens at 80°C (176°F) and melts at temperatures close to 100 to 110°C (212 to 230°F).
Bituminous Coating
Sprayed bituminous coat over sprayed zinc coating is used in Europe as well as USA for buried pipes. Zinc provides sacrificial protection. For ductile iron pipes of water systems, zinc spray-bitumastic coating is also used in combination with polyurethane or polyethylene jacketing. However, the combination is subject to failure due to scratch damage during installation.
Regulations Requiring Low Volatile Organic Compounds (VOC)
Due to EU regulations requiring zero volatile organic compounds (VOCs), new polyurethane formulation with hundred percent solid polyurethane is being offered by coating manufacturers. Polyurethane can be used for both internal as well as external surfaces. Coating can be completed during the pipe manufacturing stage itself. Zero VOC polyethylene and epoxy coatings are also being offered. Some water-based anti-corrosion coatings are also available. However, in developing country markets, solvent-based products still dominate as strict regulatory requirements are yet to be enforced in several developing countries.
Advantages of Polyurethane
Well-designed solid polyurethane reduce the load current of cathodic protection (CP)systems. A combination of polyurethane and CP is adopted in the Middle East, Asia and Europe. For corrosion protection of pipe fittings and valves, epoxy coatings are also used.
Zero VOC polyurethane coatings used for buried pipelines are an example of new coatings developed due to regulatory requirements. These coatings are used for water and wastewater piping systems, oil and gas piping and industrial applications.
Cured polyurethane is used for lining potable water pipes as well as raw water pipes, as it is inert, remains resistant to water and non-conducive to growth of microorganisms and bacteria. They are suitable for sewage pipes as well as sewage treatment systems.
Compared to traditional cement mortar lining of internal surface of potable water pipes, polyurethane lining has following advantages:
· Polyurethane is fast curing and ensures economy of high production rates and efficiency.
· Has higher adhesion to ferrous and steel surfaces. Cement mortar needs to be lined and retained in place through compression.
· Polyurethane has high impact resistance.
· Corrosion resistance of polyurethane is over 10 times higher (based on salt spray test).
· Polyurethane has higher impact resistance.
· When polyurethane is used, a smaller lining thickness is required with lower deadweight, and hence pipe design can be more efficient, reliable and economical as the wastage factor will be reduced, and pipeline capacity is higher for same size of pipe.
· Lower head loss and pumping losses due to a smoother internal surface of the pipes.
· Longer economic life as deterioration due to erosion cavitation is low.
· In the case of industrial or waste water pipes, cement mortar may get attacked by chemicals such as chlorides, whereas polyurethane has high chemical resistance, ensuring a higher economic life.
The internal corrosion of potable water piping can profoundly impact water quality due to an increase in the concentration of lead, zinc, cadmium, iron and copper, apart from pipe leaks resulting in ingress of other harmful substances due to suction effect when the system is not pressurized.
Corrosion of Gas and Oil Pipes
Internal corrosion of gas pipelines occurs when the pipe surface reacts with a combination of contaminants (e.g., moisture, oxygen, carbon dioxide, chlorides and sulfur compounds) present in gas. Operational parameters such as gas temperature, flow rate and particle velocity are also critical for corrosion prevention. Corrosion is also caused and sustained due to microorganisms when nutrients are present on the internal pipe surface.
This corrosion can be minimized by following operating guidelines for temperature and velocity parameters and contaminant control. Epoxy lining as well as polyurethane lining are used to prevent internal gas pipe and oil pipe corrosion.
Coating Selection for Oil and Gas Pipes
Polyurethane has stronger electrical properties as well as outstanding mechanical toughness together with superior corrosion resistance. Formulations of polyurethane can be customized to suit the specific application and the corrosive environment it is subjected to. Spray application technique with fast curing is an advantage, as it does not need heating before or after application. High abrasion resistance as well as impact strength can be built in specially formulated polyurethane.
Compared to polyethylene, polyurethane has better bonding reliability, and epoxy coatings suffer due to brittleness. Three-layer polyethylene with an inner epoxy coating is also used for corrosion protection of the external surfaces of pipelines. Other options such as PVC coatings as well as coal tar bitumen based coatings lose their mechanical strength as they become brittle and bonding with pipe surface too is lost due to this factor.
Telluric Currents
Telluric currents are the natural electric currents existing in the earth's crust. They are mainly induced geomagnetically (i.e., they are produced by the changes in the outer layers of the earth's magnetic field). As pipelines are constructed as electrical conductors, stretching hundreds and thousands of miles across the earth's surface, they experience electric currents induced by outside sources. These sources could be mostly man-made as in case of stray currents, or natural as in the case of telluric currents. Recent research has helped to understand the effect of telluric currents in the variations seen in values of pipe-to-soil potential. (More on this subject is available in the article Corrosion and Electrical Interference in Buried Metallic Structures.) Recent usage of high-strength and high-resistance coatings for corrosion protection has resulted in huge PSP fluctuations. The use of high strength steels in buried pipes, which are more susceptible to hydrogen on the other hand, demands stringent requirements of lower limits on PSP variations. Telluric currents influence the design of cathodic protection as well.
Stray Current Corrosion
Stray current is a major cause of corrosion of buried pipes as metallic pipe is a better conductor of current than the soil. The site at which current leaves a pipe to go back to the earth or a nearby structure will be the site of this corrosion.
Sources of stray current can be:
· New or pre-existing CP system protecting another adjacent pipe
· Direct current (DC) from transit systems in close proximity
· Power transmission systems with medium high or extra high voltages
· Sites where industrial or domestic appliances are connected to water pipes
· Welding machine ground connection with water pipes
· Induced voltage from adjacent high voltage power equipment
Cathodic Protection
Cathodic protection is a technique to control metallic corrosion, where electricity is applied in an arrangement that makes the pipeline and structures to be protected are made a cathode with respect to the ground.
When a small pipeline or a hundred kilometer long pipeline is buried in the soil, the moisture and oxygen in the soil works as the electrolyte. An anode and a cathode is formed on the same interconnected pipeline, which also forms the return path for the current.
The lower the soil resistance (due to nature of soil), the higher will be the current flow resulting in accelerated corrosion. Salt polluted ground and clay soils cause greater corrosion when compared to gravel and sandy soils. If the gravel is completely dry, then the need for cathodic protection and coatings may not arise. In steel pipes, corrosion cells could result due to manganese, iron and other contents. Even the replacement of a piece of pipe can result in anode formation with respect to existing pipe.
Every buried metal creates its own electrolyte solution potential. Thus a potential difference (voltage) is created and maintained between the ground and the pipe metal. This potential difference can be detected by connecting the negative wire of a DC voltmeter to the metal, and the positive wire to a standard electrode of copper sulfate connected electrically with the soil.
When metals are connected electrically and buried in soil underground, they spontaneously develop a galvanic cell. The metal that is higher in the galvanic series will be anodic to the other metal lower in the series. An electrochemical reaction corrodes the anode, while metal rendered cathodic is to be protected from corrosion. Normally magnesium is used as a sacrificial anode with respect to pipes and structures made of iron and steel, due to cost and stability considerations. This sacrificial anode is buried in the ground and connected electrically to the pipeline through low resistance copper wire. Multiple sacrificial anodes are used in case a single anode is insufficient.
Impressed Current Cathodic Protection
Cathodic protection with a rectifier and impressed current can replace the complicated multiple anode system, where the regular monitoring of corrosion is mandatory. Converted direct current flows from the ground bed to the piping structure and returns to ground.
The system consists of a convertor/rectifier-transformer to convert the supply voltage to the high current, low voltage DC power needed for cathodic protection. An electric cable is connected to the buried pipeline structure from the negative side of the convertor/rectifier instrument to provide a return path for the flow of electricity. Variable voltage input is provided to enable fine adjustment of the impressed current.
Impressed current cathodic protection (ICCP) has the following advantages as compared to a multiple anode system:
· It can generate a higher impressed current when a deteriorating coating is likely to accelerate corrosion.
· It can take care of any changes in soil resistivity.
· It can be adopted for coated as well as bare pipelines.
· Pipeline structures of different sizes can be protected.
Conclusion
Buried pipelines are best protected by judiciously combining coatings with cathodic protection. As far as practical, pipelines should be buried in dry crushed rock with sand. The addition of inert gases or the removal of corrosive gases and oxygen can enhance the pipeline's economic life. Attention needs to be given to flow parameters, temperatures and contaminants for both water piping systems and oil and gas pipes.