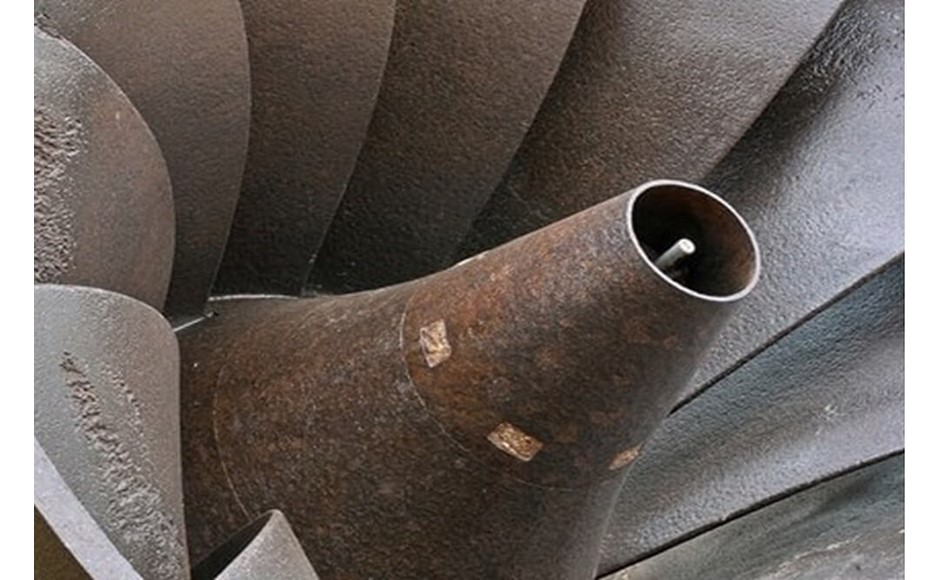
Takeaway: When dealing with fluids, cavitative and erosive corrosion are common problems. However, there are a number of solutions for dealing with them.
Cavitation takes place in a fluid system when the local fluid pressure in any region falls below the fluid’s characteristic vapor pressure, resulting in the instantaneous formation of gas vapor bubbles and gas pockets during the flow. The collapse of these gas bubbles on surfaces, later on in a high-pressure zone, causes typical cavitation corrosion as well as some erosion damage. This can be both severe and progressively disastrous. It can produce water vapor or fluid vapor at the pump suction and rapidly corrode surfaces. This can also severely affect process parameters. The pockets of steam or air that are generated in some cases can result in severe air locking, resulting in lower pump efficiency, flow volume and cooling.
The locations most susceptible to cavitation are:
·From the suction of a rotary pump, whenever it's operating at a pressure very close to the designed net positive suction head required (NPSHR)
·As a result of discharge of a throttled regulator valve, when it is at a near-closed setting
·In a system involving a sudden expansion of pipe diameter, causing considerable reduction in pressure
·At pipe joints such as bends, tee joints and elbows
Apart from cavitation, erosion of the surfaces can also occur due to corrosion debris and gritty wear debris rubbing against the surfaces.
The Basics of Cavitation
On metallic surfaces, cavitation corrosion is the result of the creation of cavities in zones of high pressure. Liquids flowing across moving elements, like propeller blades, may create steam or vapor gas bubbles at the low-pressure regions at high velocity. These steam or gas cavities form pockets in the mass of the fluid and collapse on walls and surfaces downstream, in regions of elevated pressure. The collision force of the collapsing vapor bubbles is intense enough to gouge solid particles from non-metallic and even metallic substrates.
The occurrence of cavitation is enhanced by the pre-existing, sub-microscopic vapor or gases on the subsurface. The creation of gas bubbles, at lower pressures, is dependent upon external pressure, liquid vapor pressure, the system's velocity-pressure gradient and mass density.
The extent of cavitation corrosion is also attributed to the metallurgical properties of the substrate metal. Corrosion damage can be reduced by increasing the surface hardness, by work hardening or by increasing fatigue strength . (Before selecting materials for a given application be sure to read 5 Ways to Measure the Hardness of Materials.) It has been found that decreased grain size also lessens cavitation damage. Cavitation resistance can be improved by reducing the chances of inclusions.
Chemical and electrochemical factors leading to accelerated cavitation damage have also been investigated. Seawater fluid systems have been found to be more susceptible to cavitative corrosion than freshwater systems. Cathodic protection has been deployed in many cases to neutralize the electrochemical reactions that cause the cavitation damage. Propellers of aircraft carriers and impellers of centrifugal pumps provide ready examples of cavitative corrosion. Jet aircraft are required to operate at speeds that are higher than designed speeds. Such excessive speeds have been found to result in the corrosive cavitation damage of propeller vanes. Valve seats and impellers of centrifugal pumping systems may also suffer severe cavitation damage.
Erosive Corrosion
Erosive corrosion is surface deterioration and damage due to the relative movement of an electrolytic fluid in relation to a metallic or a non-metallic substrate and in combination with an electrochemical reaction.
Turbulence caused by pits and other irregularities on the internal surfaces can result in an increase in the erosion and acceleration of failures. Factors influencing this damage include the presence of contaminants, wear debris, fluid characteristics and the flow velocity of the fluid. Induced electric current can also play a part in accelerating the damage.
The solution to this problem mostly lies in:
·Increasing the pipe's internal diameter to promote laminar flow by reducing the fluid velocity
·Using smooth coated surfaces with anti-erosion, anti-corrosion coatings or inhibitors
·Corrosion protection via cathodic protection
·Reducing gritty contaminants by providing effective filtration at different sections to arrest and evacuate the contaminant particles
Erosive corrosion is rampant in offshore drilling systems employed for crude oil and gas extraction, where sand along with the fluid flow inside the fluid system and the components are gradually deteriorated due to electrochemical reactions and the mechanical impingement of gritty sand particles. The problem can also occur in fluid-handling systems in chemical plants, power plants and hydraulic systems of mining equipment.
Designer’s Role in Preventing Cavitation Corrosion
Cavitation due to sudden pressure changes can be designed out by calculating and minimizing pressure gradients and keeping the system pressure at all regions well above the vapor pressure of the fluid. Air ingress through pipe joints and seals can be eliminated as well.
Several system operation factors and the design factors can be used to reduce cavitation in fluid systems:
·This type of corrosion can be caused by the material used and the features of the metallic surface. Damage to the surface is reduced by using suitable work-hardened materials for the surfaces.
·If possible, net positive suction head available (NPSHA) for a pump should be increased by reducing the operating temperature of the fluid. This can be done by incorporating a fluid cooler in the system if necessary.
·Some simple modifications on the pump suction side can reduce the head loss for the pump, such as by increasing the inner diameter of the suction pipe and reducing the length of the suction pipe.
·Minimize or eliminate pipe fittings at the suction side and operate the variable-speed pump at a lower speed range, wherever feasible.
·Overvoltage increases motor speed as well as connected pump speed. Voltage-limiting protection can be used to avoid overvoltages.
·Use design factors to decrease the net positive suction head required, which is dependent on:
- Size of impeller inlet
- Impeller design
- Fluid flow rate of pump
- Viscosity of fluid used and viscosity index
- RPM of the impeller
Weld Overlays
Weld overlays were the earliest methods used, but they are costly and dependent on human skill. More durable and cost-effective products are nano coatings with ceramic particles in polymers, unreinforced polyurethanes and ceramic reinforced epoxies.
Thermal Sprays
Thermal sprays of alloys such as cermets have been tried for cavitation resistance. They may result in residual stresses in the coated components and may be expensive. The density of pores and inclusions also affect the effectiveness of the protection.
Alumina-based titania coatings are also used for erosion wear resistance. They are sprayed via a high velocity oxygen fuel (HVOF) thermal process. Nano-structured agglomerated alumina-based powders are sprayed through the plasma technique. While effective erosion resistance is provided by thermal and plasma sprays, the residual thermal stresses in the components are a major disadvantage.
Polymer Coatings
The popularity of polymer coatings is due to:
·Lower labor cost and lower complexity of skills required
·Absence of residual stresses in the coated components
·Amenability for precision contours of components
Epoxy Coatings with Reinforcement
For improving the corrosive cavitation resistance of metallic substrates, polymers such as epoxies are reinforced with harder ceramic particles such as silicon carbide. These coatings have been found to be effective for low-intensity damage due to light cavitative corrosion. They are effective in the repair of cavitation damage in low-speed pump components with moderate cavitation.
Unreinforced Polymer Coatings with Polyurethane
Cavitation damage in many cases is similar to localized fatigue failures. Therefore, unreinforced polymer coatings provide much better results due to their higher flexibility. The reason that the unreinforced polyurethane-coated metallic components show better cavitation resistance than stainless steel is due to their higher capability to dissipate energy from the impinging vapor bubbles. While metals suffer permanent deformation and surface erosion, the polyurethane coating acts as a spring, cushioning the power of the micro jets of cavitation hitting the surfaces. As long as the elastic deformation of the surface does not exceed the elastic limit, there will be no damage to the surface.
Polyurethane coating materials are often produced as unreinforced as well as reinforced polymers. However, unreinforced polyurethane coatings have a greater resistance to corrosive cavitation. (To learn more about the suitability of these materials, read The Corrosion of Polymeric Materials.) Some coating producers have introduced specialized cavitation-resistant coatings. These specialized elastomeric products retain strong adhesion strength under immersion conditions, in fresh as well as seawater and other liquids, and provide a soft cushion to energy released by bubbles bursting due to high-intensity cavitation. They also provide effective resistance to corrosion and mechanical erosion.
However, when providing a coating on impeller vane leading edges, the thickness of the coat should be kept to a minimum. Otherwise, the intensity of cavitation can increase due to higher velocities induced by additional flow restrictions.
Conclusion
Whenever a fluid system experiences severe cavitation and erosion, design modifications may be carried out to reduce the intensity of cavitation and consequent damage by erosion and cavitative corrosion. The feasibility of coating the components with polymeric coatings or thermal sprays for better cavitation protection of the surfaces should also be explored for an improved cavitation protection of the surfaces.